SAP EWM Proper Guide for Optimizing Your Warehouse and Supply Chain
The intense rivalry in the e-commerce industry has placed an unparalleled burden on businesses to ensure their supply chains remain flawless. Whether managing internally or through outsourcing, businesses spend an average of €300 billion a year on warehouse management worldwide. In order to meet the expectations of modern consumers, businesses need to optimize their end-to-end warehouse management.
Effective warehouse management reduces the total time of arrival (TAT) for product delivery to customers. Warehouses are essential to the smooth operation of the supply chain because they serve as the link between the first and last miles. It is therefore essential for businesses to utilize an efficient warehouse management system to boost productivity and automate all inventory activities.
Thus, overseeing warehouses has developed into a crucial marketing tactic used by leadership teams to maximize commercial benefits.
According to Statista, the global market for warehouse automation is anticipated to reach a value of over 30 billion US dollars. According to the Zebra warehousing vision survey, over 80% of businesses globally intend to improve warehouse productivity through technology advancements. Additionally, over 27% of them have already made plans to automate their warehouse in order to improve its comprehensiveness, intelligence, integration, and cost-effectiveness by 2024.
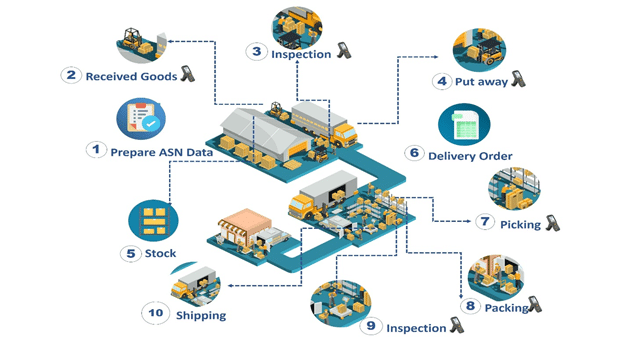
Warehousing – The Complexity
The warehouse function has changed over the past 20 years from being a simple storage procedure to a critical business component of providing a positive customer experience (CX) and keeping customers for an extended period of time.
The warehouse function has been forced to expand its bounds in terms of volumes processed and actions carried out by contemporary production and marketing trends.
The complexity of warehouse management increased along with the warehouses’ continued performance of non-traditional warehousing tasks like product processing, value-added services, cross-docking, etc., necessitating the use of an efficient warehouse management system that could optimize all aspects of the warehouse’s operations.
Why SAP EWM?
Some of the main reasons businesses select SAP EWM are to manage the operational complexity of the supply chain and to maintain the same flow of the chain around-the-clock. Companies choose SAP EWM for a variety of supply chain logistics and warehouse management-related reasons. Among the reasons are the following: an organization wants to track the precise location of its inventory throughout the supply chain; it wants to manage its inventory in a decentralized environment that can seamlessly connect with other functions of ERP for order (inbound/outbound) processing and data sharing; and more.
But the main justification for using SAP EWM is its close connection with other SAP ERP programs, such as SAP MM, SD, PP, QM, TM, and so on. non-ERP goods, such as SAP GTS, SAP CRM, and others.With its software, SAP WM, the market leader in software solutions, SAP has already demonstrated its abilities in warehouse management systems. SAP EWM (Extended Warehouse Management), a recently developed technology innovation in warehousing management, is intended to address the growing complexity of warehouse operations.
In order to address the demands of modern warehousing, SAP has created a stable, updated, and sophisticated warehouse management system. Value-added services, cross-docking, physical inventory, transportation unit management, labor management, and other areas have benefited greatly from the increased functional support.
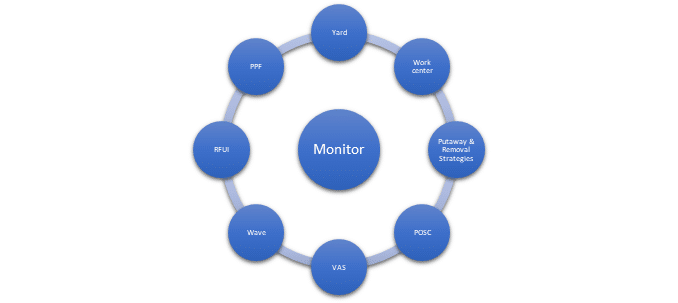
Yard Management
The yard is situated right outside the warehouse complex from the perspective of warehousing. Before being docked to the warehouse doors for loading and unloading operations, this buffer zone is used to park the trucks and transportation equipment.
A component of shipping and receiving goods is yard management, which aids in the tracking and administration of transportation units.
Various warehousing procedures are streamlined if the yard is organized in accordance with other components of the warehouse management systems. In addition to the yard, other landmarks such as parking lots, checkpoints, and entrances are designated as storage areas and bins. The ability to track inventory status from just outside the warehouse complex is made possible by yard management technology, which also streamlines productivity.
Among the many benefits of yard management are the ability to see inventory in all directions, pinpoint its precise location within the supply chain, and optimize the processing of incoming and outgoing deliveries at the transportation unit level.
Work Center to Execute the Processing Tasks
A work center is an actual warehouse space used for transitional storage between inbound and outbound activities. At this point, a number of processing tasks are completed, including packing, value-added services, deconsolidation, and quality inspection.
The Work Center’s layout can accommodate or exclude different functions, such as HU creation, Repack HU, Change HU, Deconsolidate, Quality Inspection, and VAS, based on the transactional needs.
Strategies to Optimize Putaway and Picking
Users can deliberately allow the destination bin to be determined based on product features and storage requirements during the Putaway process. In a similar vein, he can devise plans while selecting which source bin to use to choose the products for the export procedure.
Strategies choose the right bin (destination/source) in a stepwise manner based on predetermined control factors, such as process type, amount categorization, stock type, product hazard rating, etc.
Setting the various combinations of control parameters in order of priority will help further optimize this search sequence.
The Work Center’s layout can accommodate or exclude different functions, such as HU creation, Repack HU, Change HU, Deconsolidate, Quality Inspection, and VAS, based on the transactional needs.
POSC to Streamline Multi-Step Putaway or Picking Process
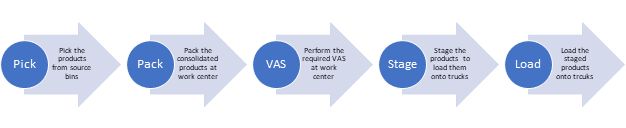
Process-Oriented Storage Control, or POSC, was implemented in EWM to simplify the intricate, multi-step putaway or pick procedure. It streamlines the procedure whereby the product passes through several processing phases, such as packing, deconsolidation, and VAS, before being deposited into the target bin.
All necessary processing steps are specified in a multistep sequential storage process within the POSC functionality, and the storage process is then allocated to the proper warehouse process type. Therefore, as soon as the activity at the first stage is completed, the system automatically advances the products to the next step in the sequence. Only goods packaged within the handling unit are compatible with the POSC feature.
VAS to Execute the Value-Added Service Tasks
Value-added tasks like labeling, adding protective packaging, oiling, and so forth are automated by VAS functionality.
Product group types and product groups are allocated to the product master records of pertinent products as part of this feature. The document type (inbound/outbound, etc.) in accordance with the VAS order to be activated is determined by the control parameters kept in the VAS relevance settings.
The VAS activity that must be carried out is specified in a package specification that is kept up to date about VAS condition type. The products are handled in accordance with the current packaging specification when the system initiates the VAS order about VAS relevant settings.
Wave to Bring Efficiency in Outbound Delivery Processing
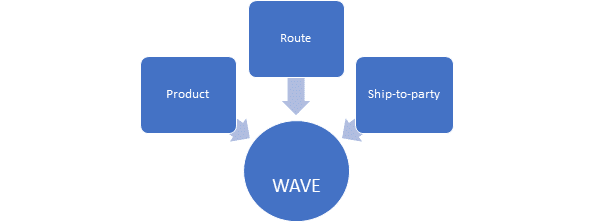
Wave capability groups outgoing delivery orders according to ship-to-party, product, and route factors, allowing them to be processed together.
When wave management is in operation, the items in the outgoing warehouse requests are sorted based on the ship-to-party, product, and route combinations. These things are then processed further to generate the warehouse tasks as a whole. More efficient use of resources and quicker order processing are the outcomes of managing the outgoing delivery orders in waves.
RF Framework for Mobile Data Capturing
We may develop and tailor the functionality of mobile data-capturing devices according to the actions of users or resources using the Radio Frequency framework that SAP offers.
Because RF devices offer mobility for data capture, using them speeds up the completion of warehouse activities. It facilitates data transfer in real time between the user and the central EWM system.
Post-Processing Framework for System Efficiency
An improvement to the SAP EWM platform is the post-processing framework. Delivery processing, shipping, receiving, printing, and initiating steps for emailing and printing labels are all done using it. It is also useful for handling the background follow-up actions (automated creation of warehousing tasks).
Workflows and subsequent tasks are automated by the actions, which are launched automatically when the conditions are met.
Monitor
With regard to EWM, the monitor serves as a dashboard providing a full 360-degree view of the movements of inventory in a warehouse, including resource management, product mastery, inbound and outgoing delivery activities, and stock availability.
Managers have good control over warehouse operations thanks to the monitor, since all data is centrally located for research and analysis.
In addition, sophisticated features like labor management monitor and assess the efficiency of the warehouse staff. It facilitates cross-docking of the products and allows the inbound delivery products to be processed straight for outgoing orders without needing to be stored.
Key Business Benefits:
With its enhanced and sophisticated functionality to optimize and automate the warehouse’s end-to-end workflows, EWM provides the company with a host of advantages.
* Task execution can be accelerated by as much as 30% using Radio Frequency Framework (RFF).
* The smooth transfer of data between RF devices and central data processing terminals is made possible by RFF.
* Automated workflows and effective resource use can lower costs and increase operational efficiency.
* WAVE feature expedites order fulfillment by up to 40%, which contributes to customer satisfaction.
* Boost resource and staff productivity by evaluating their work using labor-management features.
* The entire warehouse’s worth of merchandise and operations are visible thanks to the centralized monitoring system.
* It offers the capacity to smoothly interact with other ERP features in order to improve supply chain efficiency overall.
The “smart, best, and efficient warehouse management software that incredibly well streamlines the inventory management tool” is SAP EWM, according to Gartner.
In conclusion, a warehouse is seen as a critical component in improving the overall efficiency of supply chains in the quickly expanding supply chain industry. So, take advantage of the many advantages of warehousing and get a competitive advantage by implementing a warehouse management system. In this sense, Sap’s EWM performs exactly what is required.